
BAL CUSTOM DESIGNS
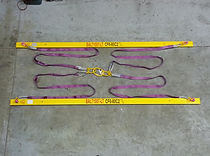
CF6 Lift and Tip 80 series

Over Wing Access Systems

T900 Transport Stand Castor Lifter
A330 APU Handling
-
Design a tailored, cost-effective solution for "shop handling" purpose
-
Collaborative design with customer
-
The solution comprised of an overhead crane attachment point.
Outcome - No requirement for a specific hoist during shop handling purposes
B737 APU Handling
-
Design a tailored, cost-effective solution for shop handling purposes
-
Collaborative design with customer
-
The solution comprised of an overhead crane attachment point.
Outcome - 1 x Tool required to attach to an APU which has traceable data vs smaller, multiple components required which were not assembled or tested.
BAL71001 - Lift and Tip (CF6-80C2)
-
Design a Lifting Device/s capable of removing a CF6-80C2 Nose Cowl from the customers furnished storage box, allowing Horizontal storage to Vertical installation
-
Customer supplied dimensions and assisted in risk analysis for the aircraft.
-
External Structural Engineer certified for ISO compliance during the inspection process
-
Varied trials completed in both vertical-horizontal and horizontal-vertical - Passed
-
Proof tested and NDT - Passed
Outcome - Safe handling and time-efficient movement of the CF6-80C2 Nose Cowl from storage to installation
BAL71001 - Lift and Tip (CF6-80E1)
-
Design a Lifting Device/s capable of removing a CF6-80C2 Nose Cowl from the customers furnished storage box, allowing Horizontal storage to Vertical installation
-
Customer supplied dimensions and assisted in risk analysis for the aircraft.
-
External Structural Engineer certified for ISO compliance during the inspection process
-
Varied trials completed in both vertical-horizontal and horizontal-vertical - Passed
-
Proof tested and NDT - Passed
Outcome- Safe handling and time-efficient movement of the CF6-80C2 Nose Cowl from storage to installation
BAL-T900C
-
Design a suitable and safe Lifting device for the T900 Castors to T900 Transport Stand·
-
Customer requirements; 1 x operator required lifting device for safe use, with minimal risk to the operator when transporting/installing.
Noted Safety concern prior to engagement of "Crush" of fingers/hands from old practices. -
External Structural Engineer certified for ISO compliance during the inspection process
-
Varied trials completed to the stand and from the stand - Passed
-
Proof tested and NDT - Passed
Outcome- 1 x Lift tool required for lifting/transport/installation of T900 Castors to Transport Stand.
BAL - B737 Wi-Fi Preload
-
Design a Lifting Beam Assy and weight configuration for preload of the Antenna and Radome seals for the B737 Wi-Fi Project
Note: 3 x Weighted and Preloaded positions required. Accuracy 1-2% of total weight for pre-load -
Calculated loads and load centres based off ViaSat supplied drawings.
-
Design a lifting beam/spreader beam assy with 3 x attachment and calibrated weights for preload.
-
External Structural Engineer certified for ISO compliance during the inspection process
-
Conducted load testing and trials of position and pre-load forces. Passed customer requirements
Outcome - Beam assy to work in conjunction with ViaSat tooling to provide pre-load of installation of Antenna and Radome assembly
BAL - QOW Safety Lanyards
-
Design a suitable solution for anchorage on all Aircraft fleet owned and controlled by the requesting customer
Note; B737, B767/A330 and B747 -
Calculated and recorded measurement for Restraint Technique of maintenance engineers to leave the Aircraft Fuselage to Wing for external inspections.
-
Design to stay within noted working surfaces for door seal inspections, without reaching FWD and Trailing Edge of wing surface
-
Confirmed with Customer for requirements during multiple trials and application use.
-
Engaged OEM (SALA) to manufacture and supply specific part numbers and quantities as required.
Outcome- Engineers are able to access the wing surface from the designated anchor point in the fuselage, and work within controlled area, with a reduction in their risk assessment.